倉庫管理とは?業務内容を徹底解説!管理に向いている人や効率的に行う方法も!
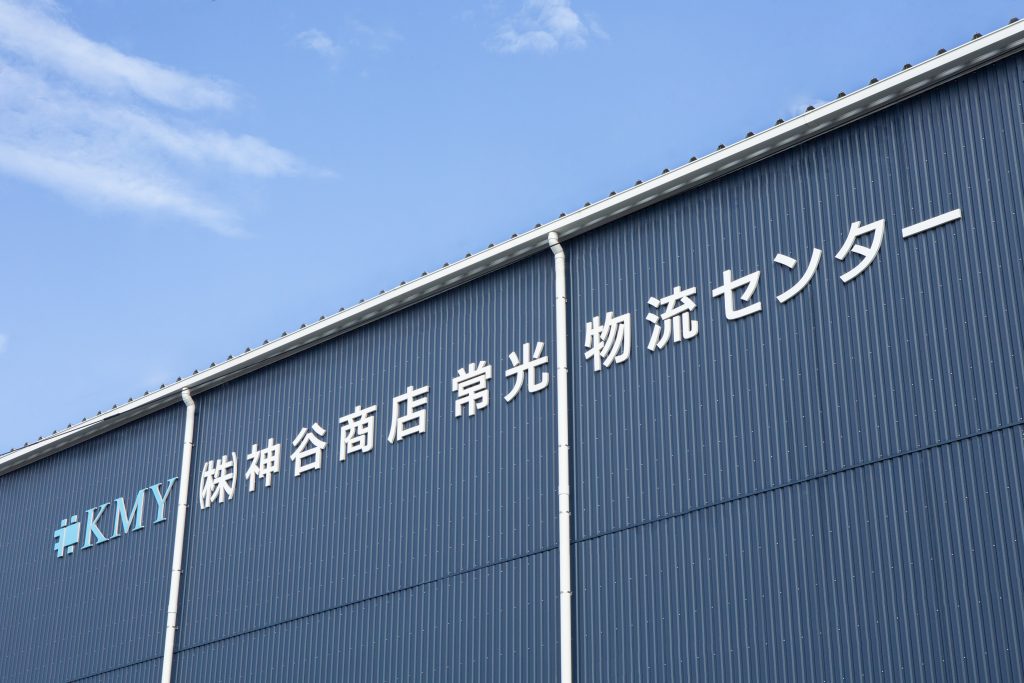
目次
- そもそも倉庫管理とは?
- 倉庫管理の業務内容
- 在庫管理の業務内容
- 倉庫管理に向いている人は?
- 倉庫管理を効率的に行うには
- 倉庫管理とは?まとめ
■そもそも倉庫管理とは?
「倉庫管理」とは倉庫内の業務をマネジメントすることを指します。具体的には在庫管理や倉庫内の人員、設備などの管理を総合的に行う業務です。倉庫管理を徹底することで出荷の遅延や誤出荷などのミスを防ぐことができ、結果としてサービス品質の向上につながります。
しかし、倉庫管理は企業が独自に標準化することが困難な業務でもあります。なぜなら、現場によって取り扱う商品の特性、保管方法、作業ルールなどが大きく異なるためです。そのため、それぞれの現場の特徴に適した倉庫管理手法を模索し、継続的に改善していく必要があります。
▶倉庫管理には「倉庫管理主任者」が必要
法律により、倉庫管理には「倉庫管理主任者」の資格を持った人間を倉庫ごとに配置することが義務付けられています。
項目 | 詳細 |
資格の種類 | 民間資格(講習受講型) |
取得方法 | 全国主要都市で実施される講習を受講 |
取得難易度 | 比較的容易(講習受講により合格可能) |
配置義務 | 倉庫1つにつき1名以上 |
▶倉庫管理主任者の主な業務内容
業務分野 | 具体的な内容 |
労働災害防止 | 作業環境の安全確保、危険箇所の特定と改善、安全教育の実施 |
倉庫適切管理 | 施設・設備の点検、温度・湿度管理、防火・防犯対策 |
運営管理 | 保管・荷役作業の監督、品質管理、作業効率の向上 |
■倉庫管理の業務内容
配送センターや倉庫において、商品の仕分け・出荷準備・保管を行う一連の作業を倉庫管理と呼びます。多くの作業が集中を要する単独作業となるため、集中力の高い人材に適した業務といえます。
必要なスキル・能力
スキル分野 | 重要度 | 詳細説明 |
体力 | ★★★☆☆ | 荷物の運搬作業。商品により負荷は変動 |
集中力 | ★★★★★ | 長時間の単独作業における品質維持 |
コミュニケーション力 | ★★★★☆ | チーム連携、情報共有、問題解決 |
責任感 | ★★★★★ | 顧客満足度に直結する品質管理 |
特別な技術 | ★☆☆☆☆ | 未経験者でも習得可能 |
▶入庫業務の流れ
商品が倉庫に届いた際の一連の作業プロセスは以下のとおりです
工程 | 作業内容 | 注意点・ポイント |
1. 荷卸し | トラックから商品を降ろす作業 | 商品の破損防止、安全な作業環境の確保 |
2. 入庫伝票照合 | 伝票内容と実際の荷物の照合確認 | 数量、品名、規格の正確な確認 |
3. 検品 | 商品の状態、品質チェック | 外観検査、機能確認(必要に応じて) |
4. 仕分け | 保管場所ごとの商品分類・配置 | 効率的な保管レイアウトの考慮 |
▶出庫業務の流れ
顧客への出荷時に実施される作業プロセスは以下のとおりです
工程 | 作業内容 | 注意点・ポイント |
1. 品出し(ピッキング) | 出荷対象商品の倉庫内からの抽出 | 正確な商品選択、効率的な回収ルート |
2. 検品 | ピッキングした商品の再確認 | 商品番号、数量、状態の最終チェック |
3. 梱包 | 適切な資材を使用した商品梱包 | 商品保護、コスト効率、環境配慮 |
4. 出荷伝票照合 | 伝票と梱包商品の最終確認 | 配送先、商品内容、数量の照合 |
■在庫管理の業務内容
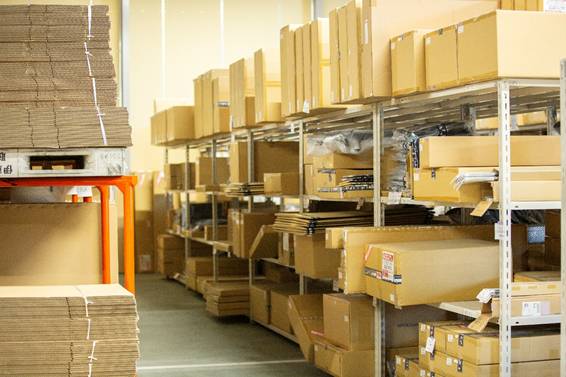
倉庫管理の中核を成す「在庫管理」とは、企業内に存在する原材料・仕掛品・製品などの在庫を、販売や生産活動に照らし合わせて最適な量と状態で供給できるよう管理することです。
▶在庫の分類と管理対象
在庫は単に販売前の製品のみを指すものではありません。将来的に現金化される可能性のあるすべての保有資産を含みます。
在庫分類 | 定義 | 具体例 | 管理のポイント |
原材料 | 商品製造に必要な基本素材 | 金属、布地、化学薬品など | 品質劣化防止、適正在庫量の維持 |
仕掛品 | 生産プロセス途中の未完成品 | 加工中の部品、組立中の製品 | 生産スケジュール管理、品質保持 |
完成品 | 販売可能状態の最終製品 | 出荷待ちの完成商品 | 需要予測に基づく在庫調整 |
補助材料 | 完成に必要な付属品・消耗品 | パッケージ材、接着剤、ラベル | コスト管理、欠品防止 |
▶在庫管理業務の詳細内容
業務項目 | 概要 | 期待効果 |
入出庫管理 | 商品の入庫・出庫データの正確な記録と追跡 | 在庫精度向上、トレーサビリティ確保 |
返品管理 | 返品商品の受付、検査、再販可否判定 | 損失最小化、品質管理強化 |
棚卸し | 定期的な実在庫と帳簿在庫の照合確認 | 在庫差異の早期発見・解決 |
ロット管理 | 製造日・消費期限等による商品グループ管理 | 品質保証、リコール対応効率化 |
これらの業務を適切に実施することで、以下のような効果が期待できます
- 業務効率の向上: 無駄な作業の削減と作業フローの最適化
- コスト削減: 過剰在庫や欠品によるロスの防止
- 品質保証: 商品の適切な保管と出荷品質の維持
- 顧客満足度向上: 正確かつ迅速な出荷対応の実現
■倉庫管理に向いている人は?
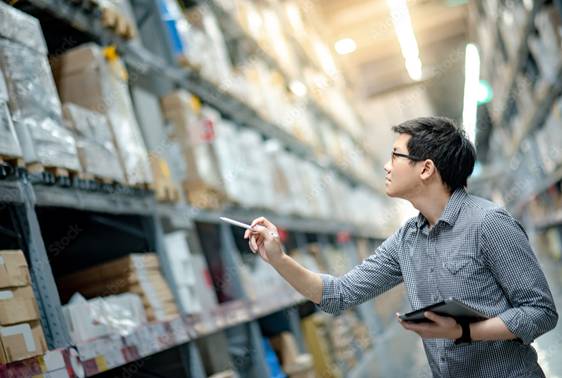
倉庫管理業務を効果的に遂行するには、複数の能力やスキルが要求されます。以下に重要な要素を詳しく解説します
▶求められる能力・特性一覧
能力・特性 | 重要度 | 詳細説明 | 業務への影響 |
体力 | ★★★☆☆ | 荷物運搬の基本的な筋力・持久力 | 作業継続性、安全性確保 |
集中力 | ★★★★★ | 長時間の単独作業における注意力維持 | 品質管理、ミス防止 |
コミュニケーション力 | ★★★★☆ | チーム連携と情報共有能力 | 作業効率、問題解決速度 |
責任感 | ★★★★★ | 顧客満足度を意識した品質管理 | サービス品質、信頼性向上 |
細かい作業への適性 | ★★★★☆ | 検品・仕分けの正確性 | 品質保証、クレーム防止 |
▶体力について
荷物を運ぶ作業が基本となるため、最低限の体力は必要です。ただし、業種によって要求される体力レベルは大きく変わります
業種・商品タイプ | 体力要求度 | 主な作業内容 | 対策・工夫 |
重量物(機械部品等) | ★★★★★ | 重量物の運搬、リフト操作 | 機械化、複数人作業 |
冷凍・冷蔵商品 | ★★★★☆ | 低温環境での長時間作業 | 防寒対策、ローテーション |
小型雑貨・アパレル | ★★☆☆☆ | 軽量商品の仕分け・梱包 | 効率的な動線設計 |
電子機器・精密機器 | ★★★☆☆ | 慎重な取り扱い、精密作業 | 専用治具の活用 |
▶コミュニケーション能力の重要性
倉庫内では想像以上に多くのコミュニケーションが発生します
主なコミュニケーション場面
- シフト引き継ぎ: 前シフトの作業状況、問題点の共有
- 緊急時対応: 設備トラブル、商品異常時の連絡・相談
- 品質問題: 検品で発見した問題の報告・対応協議
- 効率改善: 作業手順の見直し、提案事項の討議
- 安全管理: 危険箇所の共有、安全対策の徹底
▶集中力と責任感
倉庫管理業務の大部分は個人作業が占めますが、その一つ一つが最終的な顧客満足度に直結します
集中力が要求される主な場面
- 長時間のピッキング作業における商品選択ミス防止
- 検品作業での不良品・破損品の見落とし防止
- 梱包作業での適切な資材選択と丁寧な作業
- データ入力における正確性の確保
▶責任感の具体的な現れ方
- 見えない顧客のことを常に意識した品質管理
- 荷物の丁寧な取り扱いと美しい梱包
- 問題発生時の迅速な報告と改善への取り組み
- 職場環境の維持・改善への積極的参加
■倉庫管理を効率的に行うには
効率的な倉庫管理を実現するためには、物理的なレイアウト改善からデジタル技術の活用まで、多角的なアプローチが必要です。以下、具体的な改善手法を詳しく解説します。
1. 倉庫内レイアウトの最適化
倉庫内の物理的配置を改善することで、作業効率を大幅に向上させることができます。
レイアウト改善のチェックポイント
改善項目 | 現状確認事項 | 改善目標 | 期待効果 |
商品配置 | 出荷頻度と保管位置の関係 | 高頻度商品の取り出しやすい場所への配置 | ピッキング時間短縮 |
動線設計 | 作業者の移動距離・経路 | 最短ルートでの効率的移動 | 作業時間削減、疲労軽減 |
スペース活用 | 空間利用率、デッドスペース | 立体活用、通路幅の最適化 | 保管効率向上 |
作業ゾーン | 入庫・保管・ピッキング・出荷エリア | 機能別エリアの明確な区分 | 作業流れの円滑化 |
レイアウト改善の具体的手順
- 現状分析: 作業動線の可視化、ボトルネック箇所の特定
- データ収集: 商品別出荷頻度、作業時間の測定
- 改善案作成: ABC分析に基づく商品配置計画
- 試行実施: 小規模エリアでの改善効果検証
- 全体展開: 効果確認後の本格実施
2. ロケーション管理システム
どこに何が保管されているかを効率的に管理するための手法です。
管理方式 | 特徴 | メリット | デメリット | 適用場面 |
固定ロケーション | 商品ごとに保管場所を固定 | ・場所の暗記が 容易 ・新人でも対応 可能 ・ピッキング効率 が良い | ・スペース効率が悪い<br>・商品増減への対応が困難 | 定番商品中心の倉庫 |
フリーロケーション | 空いている場所に随時保管 | ・スペース効率が 良い ・商品変動に柔軟 対応 ・倉庫効率最大化 | ・位置把握が 困難 ・システム必須 ・誤配置リスク | 商品種類の多い倉庫 |
ダブルトランザクション | ピッキングと保管を分離管理 | ・両方式の利点を 活用 ・ピッキング効率と保管効率を両立 | ・補充作業が 必要 ・管理が複雑 ・初期コスト高 | 大規模・高回転倉庫 |
3. ピッキング作業の効率化
ピッキングリストの活用
従来の納品書だけでは作業効率に限界があります。ピッキングリストを導入することで大幅な改善が可能です。
比較項目 | 納品書のみ | ピッキングリスト活用 |
情報内容 | 商品名、数量、出荷先 | 商品名、数量、保管場所、優先順位 |
作業方法 | 記憶頼りで倉庫内を探索 | 指定場所への直接移動 |
所要時間 | 商品探索に多大な時間 | 最短ルートでの効率作業 |
新人対応 | 習熟に長期間必要 | 即戦力として活用可能 |
ミスリスク | 商品間違い、数量ミス | 大幅なミス削減 |
ピッキング方式の比較
方式名 | 概要 | 適用場面 | メリット | デメリット |
シングルピッキング | オーダーずつ個別処理 | 少量多品種 | シンプル、ミス特定容易 | 効率が低い |
バッチピッキング | 複数オーダーを同時処理 | 中量多品種 | 移動効率向上 | 仕分け作業が複雑 |
ゾーンピッキング | エリア別分担制 | 大量多品種 | 専門性向上、並行処理 | 連携が必要 |
4. デジタル技術の活用
バーコード・RFID技術
技術 | 特徴 | 導入コスト | 読取速度 | 読取距離 | 主な活用場面 |
バーコード | 光学式読み取り | 低 | 高速 | 接触~数cm | 一般商品管理、出荷検品 |
RFID | 電波式読み取り | 高 | 超高速 | 数cm~数m | 高価値商品、一括読み取り |
RFID(Radio Frequency ID)の特徴と活用メリット
- 非接触読み取り: 商品に触れることなくデータ取得
- 一括処理: 複数タグの同時読み取りが可能
- データ書き込み: 商品情報の更新・追記が可能
- 耐久性: バーコードより汚れ・破損に強い
近年では、スマートフォンやタブレットを活用した読み取りアプリも普及しており、導入コストの大幅な削減が可能になっています。
5. WMS(倉庫管理システム)の導入
WMS(Warehouse Management System)は、倉庫内の全業務をデジタル化し、リアルタイムで管理するシステムです。
WMSの主要機能と効果
管理分野 | 機能詳細 | 導入効果 | ROI向上ポイント |
入荷管理 | 入荷予定の事前登録、検品結果のシステム記録 | 入荷精度向上、処理時間短縮 | 人件費削減、品質クレーム減少 |
出荷管理 | 出荷指示の自動生成、進捗リアルタイム管理 | 出荷精度向上、納期短縮 | 顧客満足度向上、配送コスト最適化 |
在庫管理 | リアルタイム在庫把握、自動発注点管理 | 欠品防止、過剰在庫削減 | キャッシュフロー改善、保管コスト削減 |
返品管理 | 返品理由の分析、再販可否の迅速判定 | 返品処理効率化、損失最小化 | 廃棄コスト削減、再販機会の最大化 |
棚卸管理 | 棚卸指示の最適化、ハンディ端末連携 | 棚卸精度向上、作業時間短縮 | 人件費削減、在庫精度向上 |
帳票・ラベル | 必要書類の自動生成、即座印刷 | 事務処理効率化、ヒューマンエラー削減 | 事務人件費削減、処理速度向上 |
WMS導入の段階的アプローチ
導入段階 | 実施内容 | 期間目安 | 重要ポイント |
Phase 1 | 基本機能(入出庫管理)の導入 | 3-6ヶ月 | 既存業務フローとの整合性確保 |
Phase 2 | 在庫管理・ロケーション管理の統合 | 6-9ヶ月 | データ精度の向上と運用定着 |
Phase 3 | 高度分析機能・他システム連携 | 9-12ヶ月 | 経営判断に活用できるデータ分析 |
WMS選定時の重要な評価項目
評価項目 | 重要度 | チェックポイント |
機能適合性 | ★★★★★ | 自社業務フローへの適合度、カスタマイズ性 |
操作性 | ★★★★☆ | 直感的な画面設計、習得の容易さ |
拡張性 | ★★★★☆ | 将来的な機能追加、他システム連携の可能性 |
保守・サポート | ★★★★☆ | ベンダーの対応体制、運用支援の充実度 |
導入コスト | ★★★☆☆ | 初期費用、月額費用、ROIの妥当性 |
■倉庫業とは?まとめ
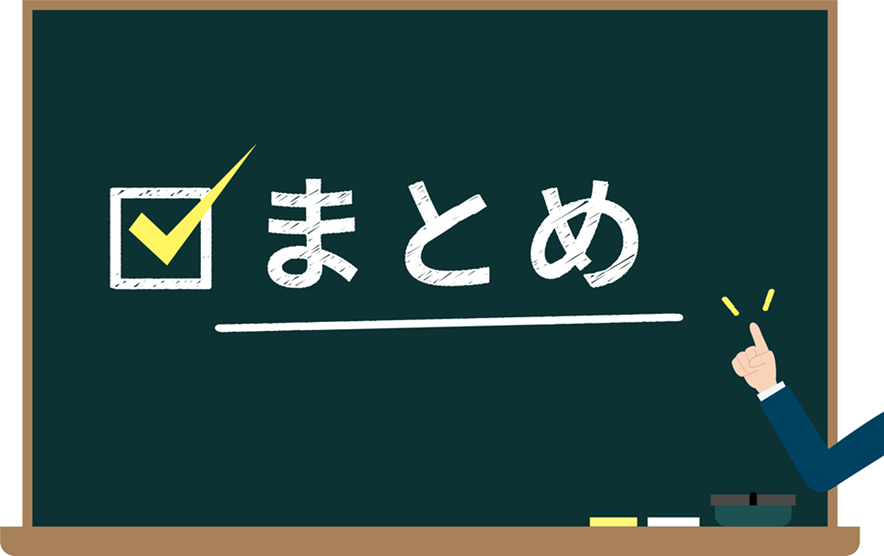
現代の倉庫業界では、荷物取扱量の急激な変化や慢性的な人手不足といった課題に直面しており、従来の勘と経験だけに頼った倉庫管理では限界があります。こうした状況下において、効率的な倉庫管理業務を実現するためには「倉庫業務の見える化」を推進することが極めて重要になっています。
▶今後の倉庫管理に求められる視点
1. データドリブンな経営判断 倉庫が大規模化し、取り扱い商品が多様化するほど、データに基づいた科学的な管理手法が不可欠となります。WMS等のシステムを活用してリアルタイムデータを収集・分析し、客観的な改善点を特定していくことが重要です。
2. 人的リソースの最適化 人手不足が深刻化する中、限られた人員で最大の成果を上げるためには、作業の標準化と効率化が必須です。個人の経験やスキルに依存しない仕組み作りを進めることで、新人でも即戦力として活躍できる環境を整備する必要があります。
3. デジタル変革への対応 単純にシステムを導入するだけでは効果は限定的です。重要なのは、導入したWMSやRFID等の技術を通じて収集されるデータを分析し、現状の課題や改善ポイントを明確に把握することです。
成功に向けた具体的なアクションプラン
フェーズ | 実施項目 | 期待される成果 | 成功のカギ |
基盤整備 | ・現状業務の可視化 ・基本的な5S活動 ・作業標準の策定 | ・作業品質の安定化 ・ムダな作業の削減 | 全従業員の意識改革と継続的な改善活動 |
システム化 | ・WMS等の導入 ・バーコード/RFID活用 ・データ収集体制構築 | ・リアルタイム管理の 実現 ・ヒューマンエラーの 削減 | 段階的導入と十分な教育・訓練 |
高度化 | ・データ分析による 改善 ・予測機能の活用 ・他部門との連携強化 | ・予防的な問題解決 ・経営戦略への貢献 | 分析結果を実際の改善行動に結びつける仕組み |
▶最終的な目標
効率的な倉庫管理を実現するためには、単なる作業効率の向上だけでなく、倉庫管理業務のどこにボトルネックがあり、どのような改善を行えば全体最適につながるのかを継続的に分析・検証できる体制を構築することが重要です。
このような分析と改善のサイクルを回し続けることで、変化する市場環境や顧客ニーズに対応できる柔軟性のある倉庫管理システムを確立し、長期的な競争優位性を築いていくことが、今後の倉庫管理効率化における最大の課題であり、同時に最大の機会でもあるのです。
↓↓お問い合わせはこちら↓↓